HVAC anomolies: Prevention is better than cure
Fault Detection and Diagnosis (FDD) in HVAC systems has become an increasingly important area of research and development in recent years, thanks to powerful monitoring software coupled with artificial intelligence. This detection generally relies on measurements of variables available in a control system, including temperatures (heating and cooling systems), energy consumption (electricity, gas, or other sources), and pressures (water supply).
The earlier the detection of any emerging issue, the easier it will be to avoid extended battery downtime periods or even prevent more serious and costly damage.
Thermal management system failures were found in 15% of audited BESS units, typically manifesting as coolant leaks from poorly secured pipes, faulty temperature sensors, or malfunctioning circuit boards. These issues increase the risk of overheating, potentially leading to thermal runaway – a hazardous condition that can cause battery fires.
Solar Risk Assessment 2005/kWH analytics
HVAC System overview: Heating, Ventilation, and Air Conditioning – prerequisites for high-performance energy storage systems
The HVAC system is a thermal regulation system used for electricity storage battery containers. Its role is to control the interior temperature of a given space, including both heating, cooling and ventilation to ensure optimal temperature quality. HVAC stands for “Heating, Ventilation, and Air Conditioning.
This HVAC system relies on sensors to measure temperature and automatically adjust heating and cooling based on user preferences. For batteries, the HVAC system assures long term maintenance by identifying and setting optimal temperature ranges. These temperatures help prolong the life of the batteries and ensure operational safety. This range is generally around +25°C/ ± 5°C (+77°F /± 5°F). It also serves to “chill” the cooling system to prevent potential damaging overheating.
Figure: Example of an HVAC system
Why is HVAC critical to the operational success of battery storage platforms and associated battery infrastructure?
Heating, air conditioning, and cooling can represent a significant part of a battery container’s consumption. It is often the main source of energy consumption, particularly if the system operates in geographic areas with extreme climates or in data centres which rely on batteries designed to work within a specific temperature range to perform correctly.
When problems occur in these complex systems, they often may not be diagnosed immediately. During this time period, where no corrective measures are carried out, costly energy losses can occur as well as potential damage to batteries, significantly impacting their lifespan.
HVAC pain points: What anomalies are observed?
HVAC system anomalies are recurrent. They cause an increase in battery temperature related to usage, known as the “Joule effect”, namely heating related to the passage of charge/discharge current. Without regulation and with intensive use such as those encountered in stationary applications, the temperature drifts upwards without the BMS (Battery Management System) control system detecting an anomaly because the temperature remains below critical temperature thresholds from a safety perspective.
The system then operates at higher temperatures than it should. This has a notable impact on battery life. Operators generally only notice this when the BMS detects the safety temperature threshold and performs its cutoff role.
In the case of a combined HVAC and BMS anomaly, this can have even more serious consequences, such as starting a fire. Indeed, without stopping usage at the critical temperature (around 50°C), the system continues to drift until reaching the thermal runaway temperature (generally above 90°C and dependent on battery chemistry).
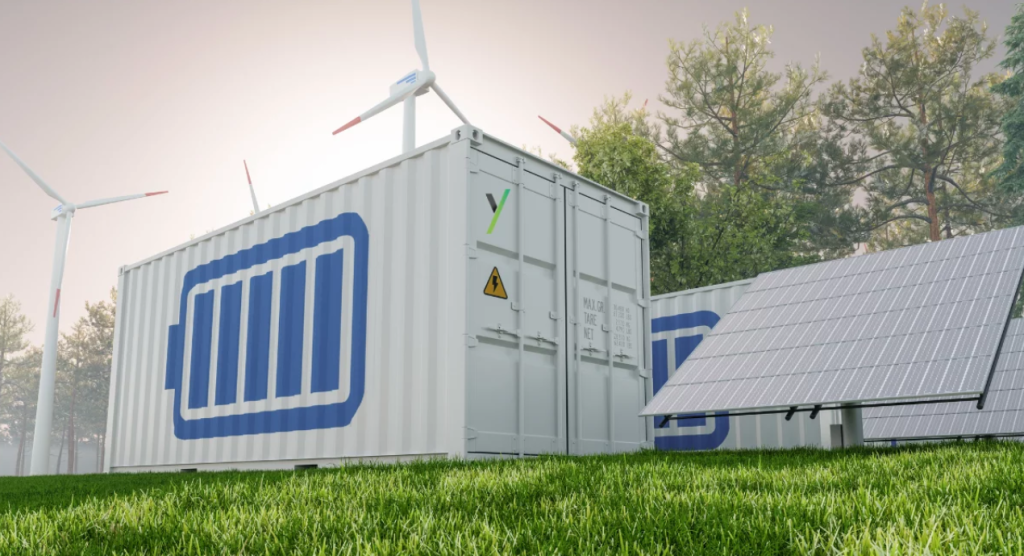
Early detection: Essential first steps to prevent thermal runaway
It is therefore essential to detect issues as soon as possible (within a day), without waiting for the system to drift over one or more weeks before reaching the safety threshold and a system shut down for maintenance. This early detection from the first day of an anomaly is fundamental to a swift and safe resolution.
Nip it in the bud: How PowerUp’s marriage of electrothermal modelling and machine learning identifies HVAC anomalies, quickly and accurately
Thanks to the increasing availability of battery analytics solutions like those from PowerUp, which combine Machine Learning and electrothermal modelling of batteries, the system becomes capable of quickly and automatically diagnosing any problems that arise. This then helps maintenance operators to take corrective action to ensure the proper safety and performance of the HVAC system and, consequently, the batteries.
Learn. Detect. Inform: How Powerup’s battery analytics solution safeguards your energy storage system
During the learning phase, the algorithmic solution identifies all model parameters. Once the learning phase has been completed (usually less than a month of data collected in real-time operation), the model verifies thermal behaviour and alerts users in case of any detected anomaly, allowing the identification of any HVAC issues from day one.
These results have been validated on a wide range of data, including different battery chemistries, different cell suppliers, different integrators, and different thermal management systems. Furthermore, the learning model continues to learn throughout the battery’s usage, automatically adapting to any change in usage, such as any change in the temperature setpoint of the HVAC system, for example.
The foresight awarded by PowerUps battery analytics solutions results in considerable gains and helps minimize the impact on battery life (due to high temperatures) and minimize (or even avoid) the risk of service interruption (which is currently linked to reaching the critical safety threshold). Another key benefit: PowerUp’s solutions are not dependent on any specific thermal management solution. Whether it’s “air-cooling” or “liquid-cooling,” the detection model works in the same way.
How it works: Operational case study
Figure: Temperature profile of a rack in a container without management issues (Container 03 Rack 01), superimposed with that of a rack in a container experiencing an air conditioning failure (Container 04 Rack 01).
This figure illustrates the case of an air conditioning problem encountered in a container, which led to temperature drift across all racks in this container (shown here by Rack 01 of Container 04), while the rest of the assets with the same usage profiles did not experience thermal management issues (shown here by Rack 01 of Container 03).
- In this example, the temperature drift extended over 10 days, with operating temperatures between 30°C and 50°C (harmful to equipment lifespan), before reaching the shutdown threshold for thermally unregulated racks (here at 55°C).
- The service interruption of Container 04 furthermore caused the shutdown of other containers at the site connected to the same delivery point (illustrated by the shutdown of Container 03 on February 19, which was not affected by the temperature regulation problem).
- Finally, this example shows that the return to normal operation occurred after two days of general interruption, which could have been avoided by detecting the anomaly from the first day. This is made possible by the automatic analysis module developed by PowerUp.
HVAC fault detection – prevention is better than cure
In conclusion, the integration of advanced HVAC fault detection and diagnosis (FDD) protocols, powered by AI-driven analytics like those of PowerUp, is crucial for ensuring the safety and optimal performance of battery storage systems. Early detection of HVAC anomalies, within a day, prevents costly energy losses, extends battery lifespan, and mitigates the risk of catastrophic failures like thermal runaway.
By leveraging electrothermal modeling and machine learning, these solutions provide the foresight needed to proactively address issues, ultimately safeguarding energy storage investments and minimizing operational disruptions.
If you want to find out more about PowerUp can help you increase the safety, performance and sustainability of your platform, contact us
Other articles of interest
You may be interested in the following articles
- How to safely make the most of BESS performance CLICK HERE
- Zoom on cell imbalance – Predictive safety management CLICK HERE
- BMS vs Cloud Analytics CLICK HERE